More Than Just a Broken Part: Analysis of Mechanical Failures
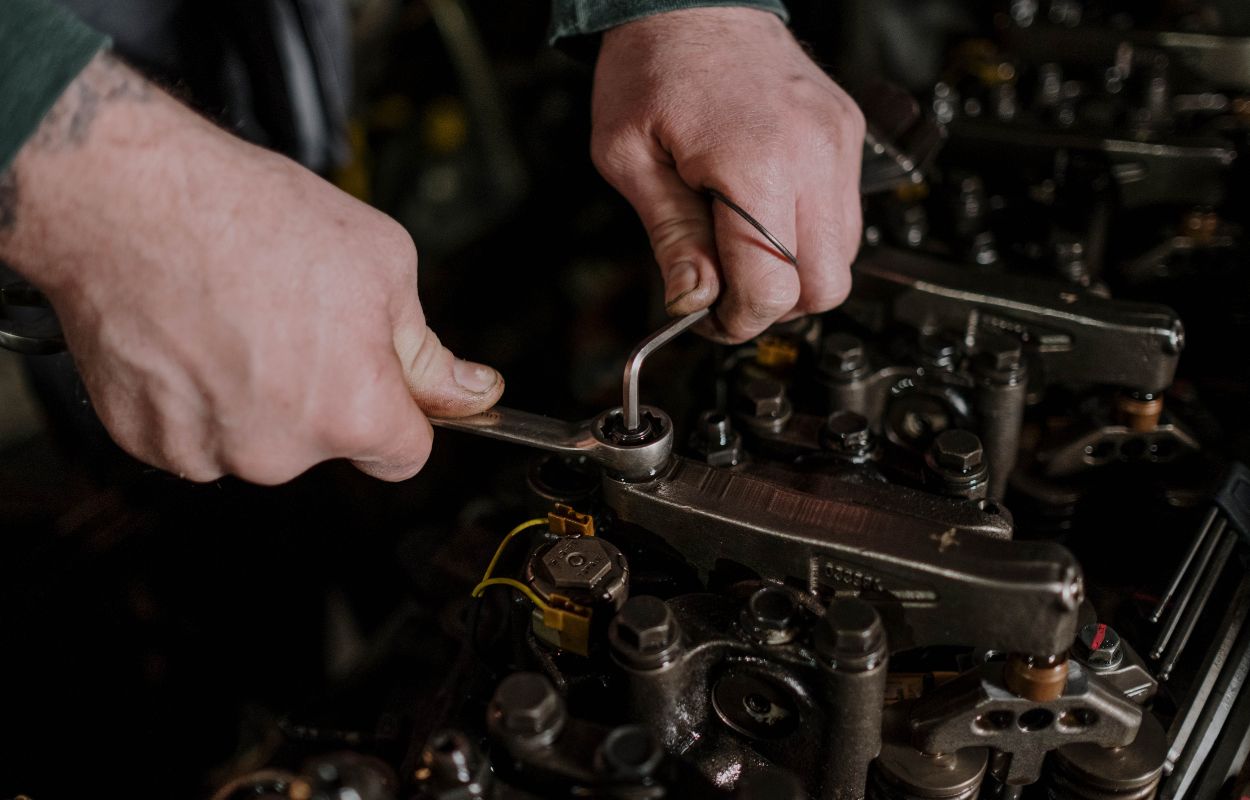
There are numerous reasons why a product part might fail during use. While witness statements can provide some insight into what occurred during an incident, a mechanical engineer’s analysis can determine the specific cause of the failure and other contributing factors. Several of the most common factors in mechanical failures are discussed below.
Manufacturing defects or errors: Simply put, a manufacturing error occurs when the product does not match the design. These are often due to components that are out of tolerance, use of the wrong material, or manufacturing/assembly equipment that has not properly adjusted or maintained.
Design defects or errors: Design defects may result from a failure to identify the way the product will be loaded under reasonable use, or a failure to use adequate factors of safety to account for normal variations in the loading, material properties, manufacturing, or numerous other factors.
Improper or inadequate maintenance: Most products will need some level of maintenance to function properly for their lifetime. If this maintenance is neglected or performed improperly, the product is more likely to sustain excessive wear or damage and its ability to safely function as intended will decrease. Improper or inadequate maintenance includes failure to routinely inspect the product, to identify and repair normal or unusual wear or damage.
Improper material or poor selection of materials: A product may fail to perform its intended function due to an incompatibility of materials with the environment. Examples include the use of untreated steel in a wet or damp environment or the use of a materials in an application where it would be exposed to a substance that would degrade it. In some cases, this is due to the selection or specification of a product without adequate consideration of its compatibility with the environment where it is to operate.
Improper heat treatments: Materials are heat-treated to alter their physical or chemical properties. The product is heated and cooled to specific temperatures, sometimes at specific rates, to have the desired effect. Improper heat treatment can result in substantially different properties.
Casting defects: Voids, contaminations, discontinuities, or other imperfections can alter the properties of a molded product. While some defects are apparent on the object’s exterior or by microscopic inspection, others might require non-destructive examination, such as an x-ray or ultrasonic inspection. In some cases, destructive testing of the object may be the only way to identify the defect.
Misuse or abuse: Failure may result when a product is improperly loaded, resulting in excessive stress. In some cases, the misuse should be apparent to a user, while other times the misuse is something many people would not see as improper. When the misuse is not readily apparent to the user, there may be a question of the presence or effectiveness of warnings and/or instructions.
Assembly errors: Errors in assembling products can occur at various points in the supply chain, from the manufacturer, importer, supplier, delivery company or end user. Once improper assembly is identified as a factor in a product failure, the next goal is to determine who was responsible for assembly of the failed part(s).
Lack of quality control or assurance: While many of the previously discussed defects may be expected, use of a robust inspection or quality control process should help identify problems early and help prevent the defects from entering the stream of commerce.
Inadequate safeties: Products should be designed with features to help protect users and property from damage. While not entirely foolproof, interlocks, guards or limit switches are useful in preventing mishaps.
Unforeseen issues: Mishaps can occur when all the proper steps were taken, especially if the product was used in a way that was not anticipated. Consumers will find new, inventive, and unforeseen ways to use (or misuse) a product which may lead to an incident or failure. In these cases, the primary issue may relate to the adequacy of the instructions and warnings, requiring analysis of whether the alternative use was within the allowable or reasonably expected uses.
When there is an allegation that a failure may have contributed or had a role in an incident, having a failure analysis performed by a mechanical engineer is one of the best ways to determine the potential case issues.